In today’s construction industry, managing supply chain challenges is crucial to keeping projects on track. Whether you’re a custom home builder, general contractor, or project manager, dealing with supply chain disruptions can be tough. From material shortages to shipping delays, these issues can seriously affect project timelines, costs, and overall success. APB reports that with supply chain constraints easing, more projects were finished on time or even early—an improvement from previous years when delays were more common. However, 28.6% of projects still experienced delays, mainly due to subcontractor-related problems.
From material shortages to shipping delays, these challenges can significantly impact project timelines, costs, and overall success. However, with the right strategies and tools, you can mitigate these issues and ensure your projects stay on schedule.
Understanding the Supply Chain Challenges
The construction supply chain is complex, involving numerous stakeholders, from material suppliers to logistics providers. Recent global events, such as the COVID-19 pandemic, geopolitical tensions, and fluctuating demand, have exacerbated existing supply chain vulnerabilities. Builders now face:
- Material Shortages: Essential materials like lumber, steel, and concrete are often in short supply, leading to price spikes and delays.
- Transportation Delays: Port congestion, trucking shortages, and increased demand have slowed down the delivery of critical materials.
- Labor Shortages: Skilled labor is increasingly hard to find, causing delays in production and assembly.
- Regulatory Changes: Tariffs, import/export restrictions, and changing environmental regulations can disrupt the supply chain.
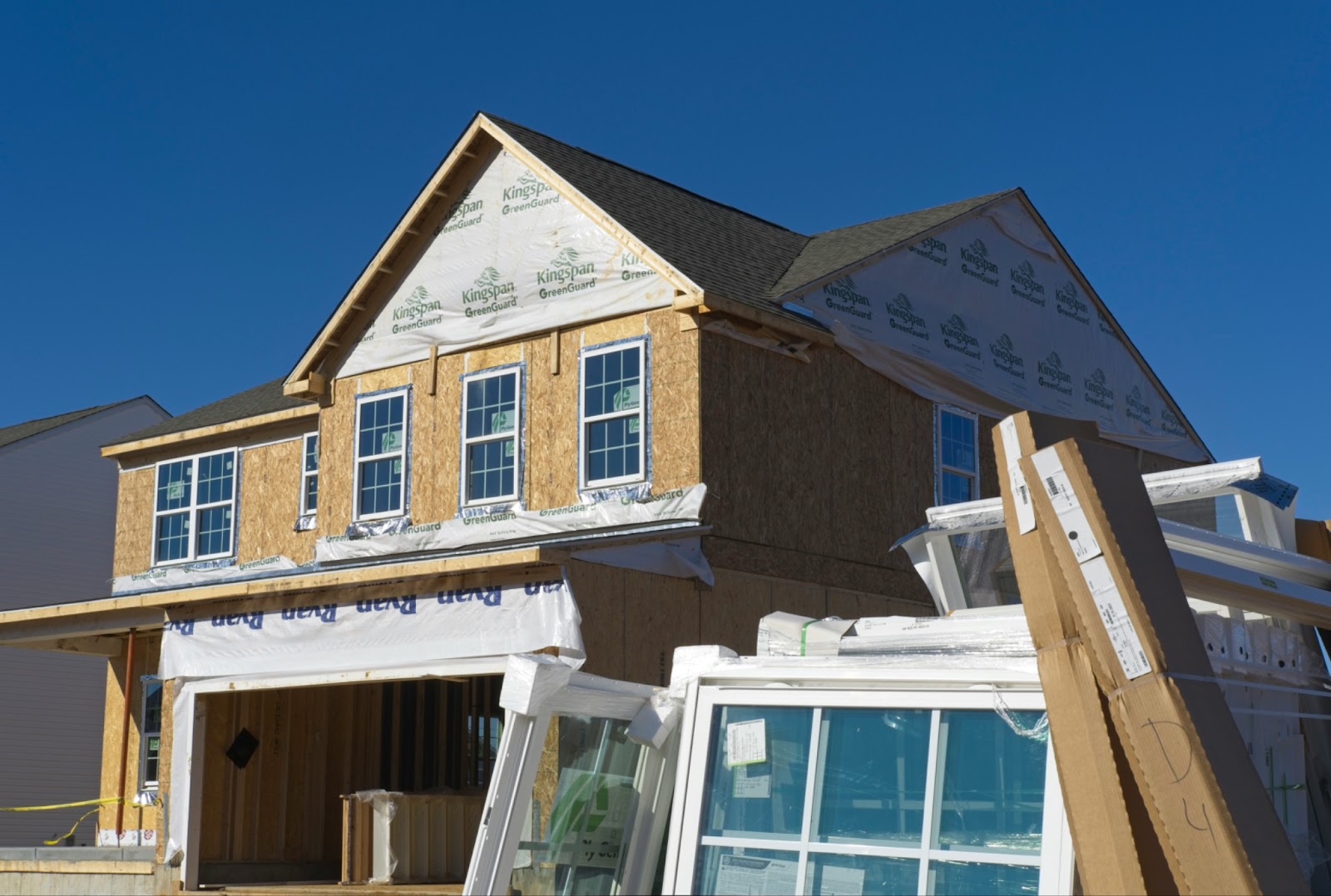
Proactive Planning and Communication
One of the most effective ways to manage supply chain challenges is through proactive planning and communication. This involves:
- Advanced Procurement Planning: Order materials well in advance to account for potential delays. Partner with suppliers who have a track record of reliability and flexibility.
- Diversified Supplier Base: Avoid relying on a single supplier. Diversify your supplier base to reduce the risk of shortages.
- Transparent Communication: Keep all stakeholders informed about potential delays and changes in the project schedule. This includes regular updates to clients, subcontractors, and suppliers.
Leveraging Technology to Stay Ahead
Technology can be a game-changer in managing supply chain challenges. Platforms like Digs provide builders with tools to streamline communication, track orders, and manage projects in real-time. Here’s how technology can help:
- Real-Time Tracking: Use construction management software to monitor the status of orders, deliveries, and inventory levels. This allows you to quickly address issues as they arise.
- Document Management: Centralize all project-related documents, including contracts, purchase orders, and shipping receipts, to ensure everyone is on the same page.
- Collaboration Tools: Facilitate communication between all parties involved in the project, from suppliers to clients, through a single platform. This ensures that any changes or updates are immediately shared with the team.
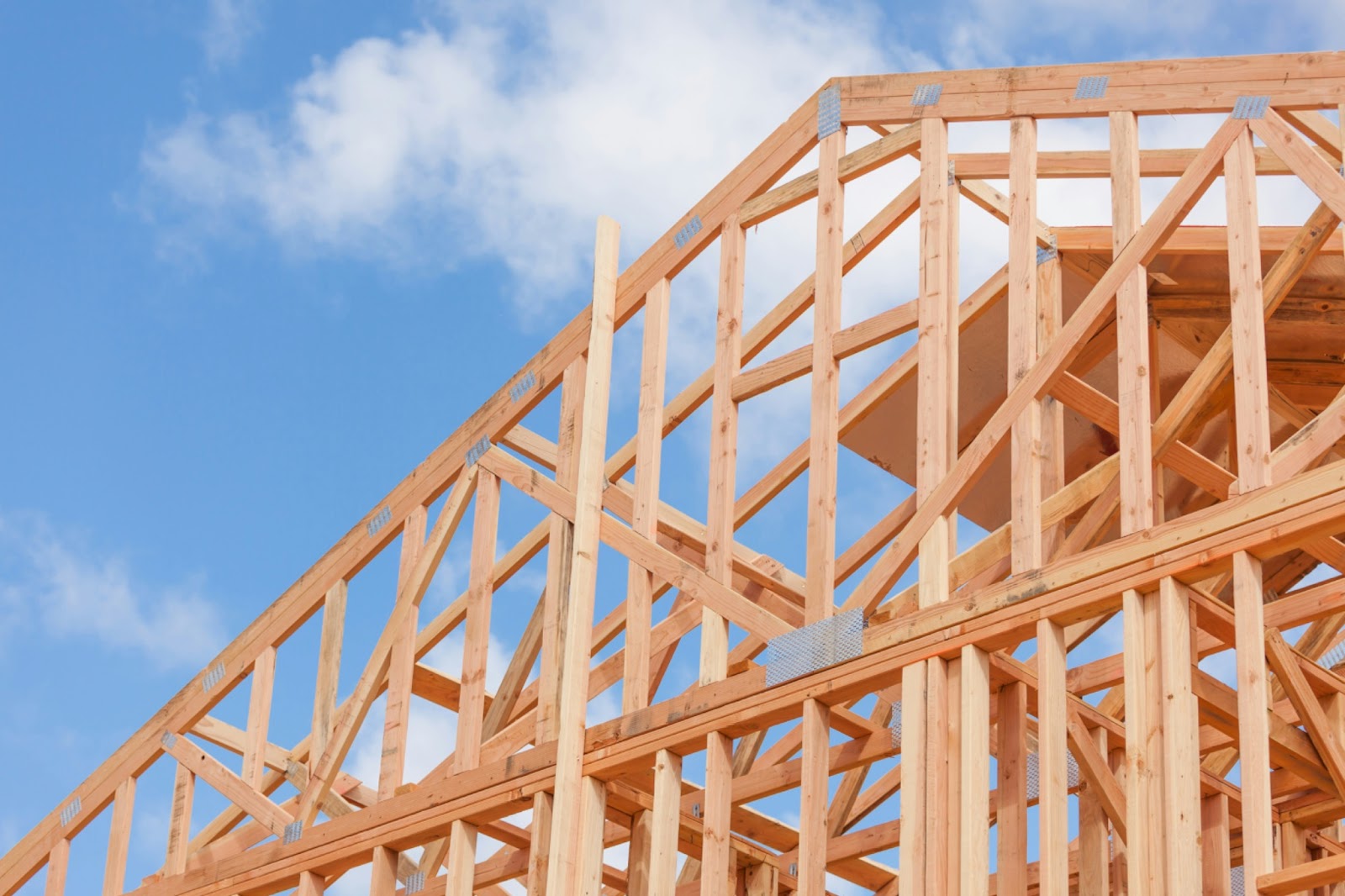
Building Strong Relationships with Suppliers
Strong relationships with suppliers can make a significant difference in how supply chain challenges are managed. Consider these tips:
- Long-Term Partnerships: Build long-term relationships with key suppliers. They are more likely to prioritize your orders and work with you to find solutions when issues arise.
- Flexibility in Contracts: Negotiate flexible terms in your contracts that allow for adjustments in delivery schedules and prices due to unforeseen supply chain disruptions.
- Regular Performance Reviews: Regularly review your suppliers' performance to ensure they meet your quality and delivery standards.
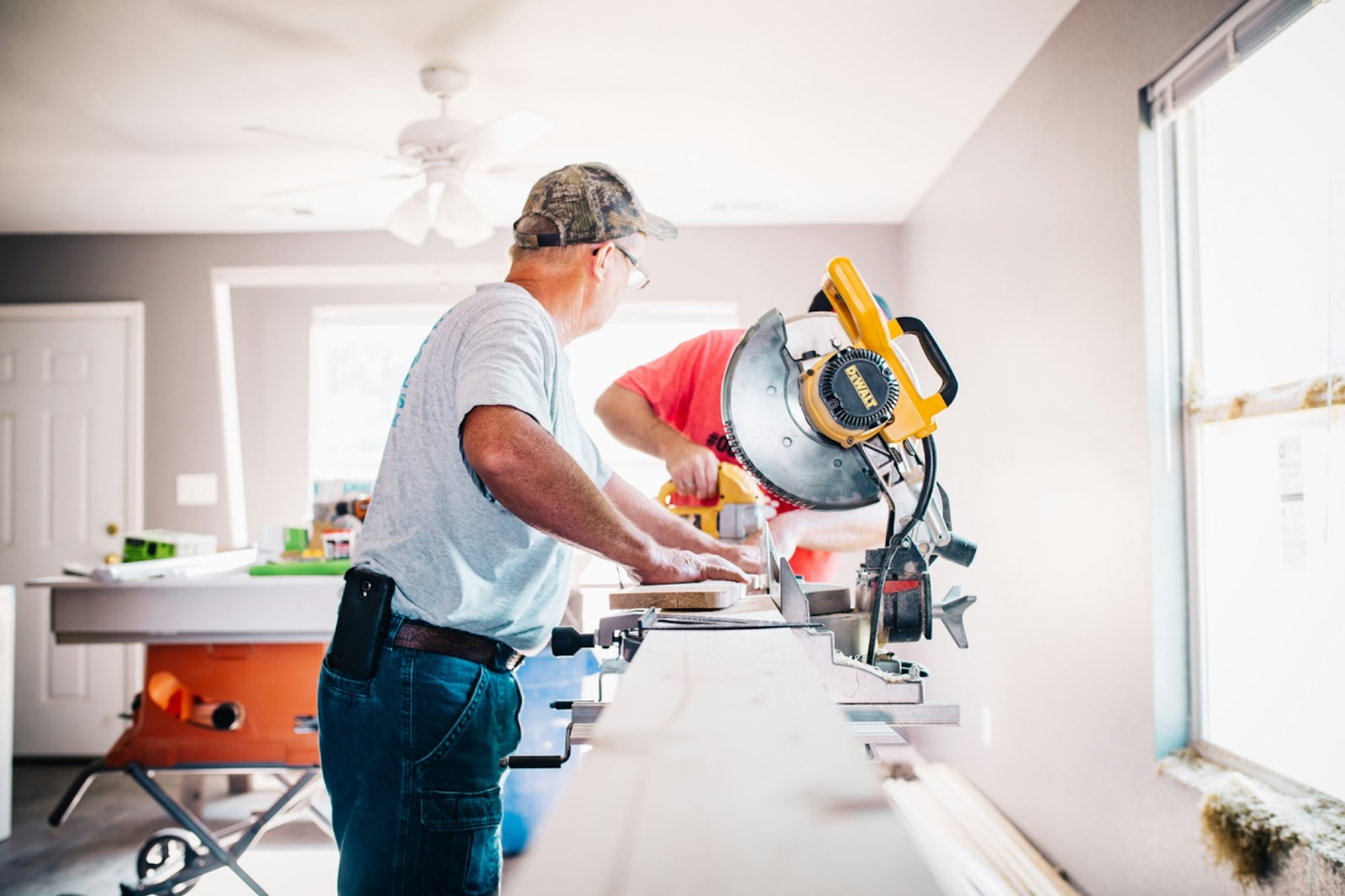
Contingency Planning
No matter how well you plan, unexpected supply chain challenges can still occur. Having a contingency plan in place can help minimize the impact on your project. This includes:
- Buffer Stock: Maintain a buffer stock of critical materials to cushion against sudden shortages.
- Alternative Materials: Identify alternative materials or products that can be used if your preferred options are unavailable.
- Flexible Scheduling: Build flexibility into your project schedule to accommodate potential delays without significantly affecting the overall timeline.
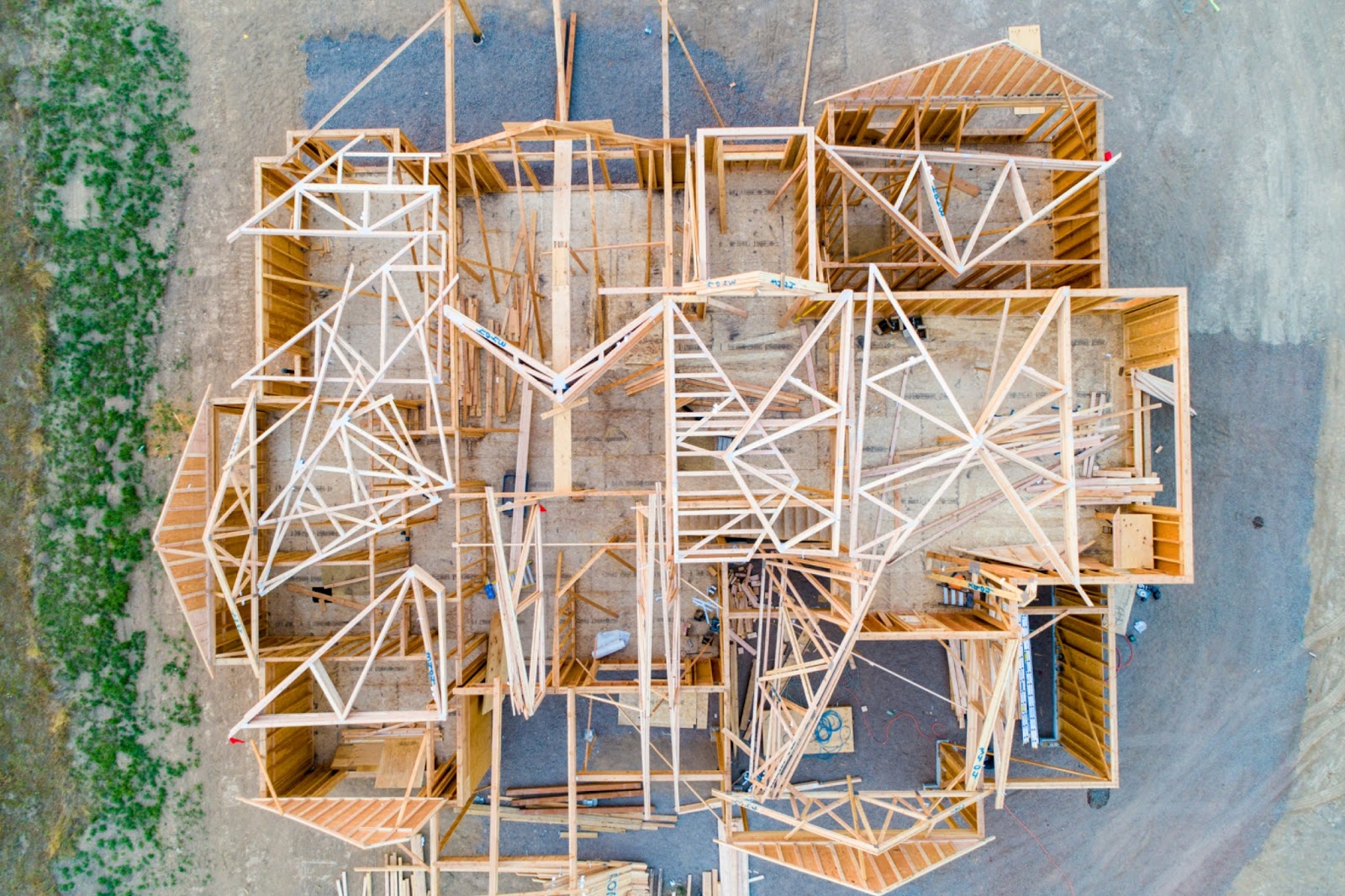
Managing supply chain challenges in construction requires a combination of proactive planning, strong relationships, and the effective use of technology. By staying ahead of potential issues and having contingency plans in place, you can keep your projects on track, even in the face of supply chain disruptions. Tools like Digs can play a crucial role in streamlining communication and managing the complexities of today's supply chains, ensuring that your projects are completed on time and within budget.
Digs is a collaboration software solution for home builders, vendors, and homeowners that provides more efficient file storage, collaboration, and homeowner handoff for home construction projects.
Unlock a happier home at Digs.com